Discover What is Porosity in Welding and Its Effect on Structural Integrity
Wiki Article
The Scientific Research Behind Porosity: A Comprehensive Overview for Welders and Fabricators
Understanding the detailed devices behind porosity in welding is essential for welders and producers striving for impeccable workmanship. From the composition of the base materials to the complexities of the welding process itself, a wide variety of variables conspire to either exacerbate or ease the visibility of porosity.Comprehending Porosity in Welding
FIRST SENTENCE:
Evaluation of porosity in welding discloses crucial insights right into the stability and high quality of the weld joint. Porosity, identified by the existence of cavities or gaps within the weld metal, is a common problem in welding procedures. These voids, otherwise properly attended to, can endanger the architectural integrity and mechanical residential or commercial properties of the weld, bring about prospective failures in the ended up product.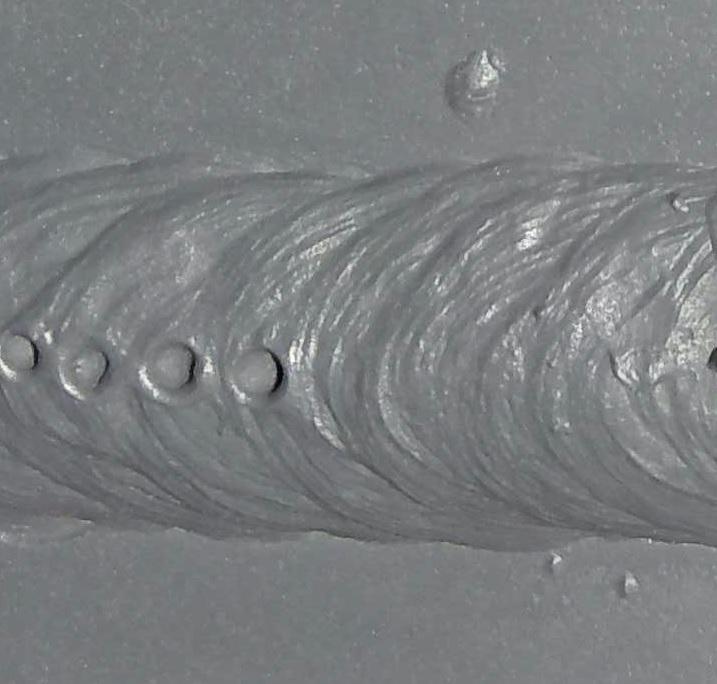
To detect and evaluate porosity, non-destructive testing techniques such as ultrasonic testing or X-ray evaluation are usually used. These methods enable the identification of inner defects without compromising the integrity of the weld. By assessing the dimension, form, and circulation of porosity within a weld, welders can make educated decisions to enhance their welding processes and accomplish sounder weld joints.
Aspects Affecting Porosity Formation
The incident of porosity in welding is influenced by a myriad of aspects, ranging from gas securing effectiveness to the intricacies of welding specification setups. Welding specifications, consisting of voltage, existing, take a trip speed, and electrode kind, likewise impact porosity development. The welding method utilized, such as gas steel arc welding (GMAW) or protected steel arc welding (SMAW), can affect porosity formation due to variations in warm circulation and gas protection - What is Porosity.Effects of Porosity on Weld Top Quality
Porosity formation considerably endangers the structural honesty and mechanical properties of welded joints. When porosity is present in a weld, it produces gaps or cavities within the product, decreasing the general toughness of the joint. These voids serve as stress focus points, making the weld a lot more vulnerable to cracking and failure under lots. The visibility of porosity also deteriorates the weld's resistance to corrosion, as the entraped air or gases within deep spaces can respond with the surrounding setting, bring page about degradation over time. In addition, porosity can prevent the weld's capacity to endure stress or effect, more endangering the overall top quality and integrity of the bonded framework. In essential applications such as aerospace, vehicle, or structural building and constructions, where safety and security and longevity are vital, the destructive results of porosity on weld quality can have serious repercussions, highlighting the significance of decreasing porosity with appropriate welding methods and treatments.Strategies to Lessen Porosity
Furthermore, utilizing the appropriate welding criteria, such as the appropriate voltage, present, and travel speed, is important in preventing porosity. Preserving a consistent arc length and angle during welding likewise assists decrease the chance of porosity.
In addition, selecting the right securing gas and preserving proper gas circulation prices are essential in lessening porosity. Making use of the suitable welding method, such as back-stepping or utilizing a weaving movement, can likewise aid distribute warm equally and lower the opportunities of porosity development. Ensuring appropriate air flow in the welding atmosphere to get rid of any type of possible resources of contamination is vital for achieving porosity-free welds. By this contact form executing these techniques, welders can successfully minimize porosity and create high-quality welded joints.

Advanced Solutions for Porosity Control
Carrying out cutting-edge modern technologies and cutting-edge methods plays a critical function in accomplishing superior control over porosity in welding procedures. One sophisticated solution is the use of sophisticated gas blends. Securing gases like helium or a mixture of argon and hydrogen can assist minimize porosity by providing far better arc security and boosted gas coverage. In addition, utilizing innovative welding methods such as pulsed MIG welding or changed ambience welding can likewise help mitigate porosity concerns.Another innovative solution entails making use of sophisticated welding equipment. Making use of devices with built-in attributes like waveform control and sophisticated power resources can boost weld high quality and lower porosity threats. Moreover, the application of automated welding systems with specific control over parameters can considerably decrease porosity defects.
Furthermore, incorporating advanced tracking and inspection innovations such as real-time X-ray imaging or automated ultrasonic testing can aid in spotting site here porosity early in the welding procedure, permitting instant restorative activities. Generally, incorporating these sophisticated solutions can considerably boost porosity control and boost the general top quality of bonded elements.
Final Thought
In conclusion, comprehending the science behind porosity in welding is crucial for welders and fabricators to create top quality welds - What is Porosity. Advanced options for porosity control can additionally enhance the welding process and make certain a solid and dependable weld.Report this wiki page